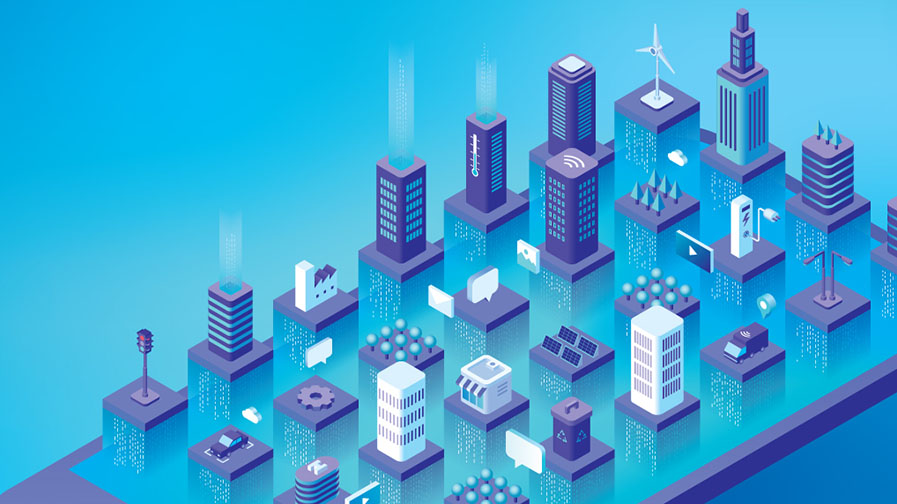
Posted on Reading Time: 5 minutes
onIt’s always exciting to see how MEF 3.0 is impacting our everyday lives. The MEF 3.0 PoC (126) 5G Factory—Private Enterprise Networks for Industry 4.0—is clearly one of those examples. For those that don’t know what Industry 4.0 means, it is the title of the latest generation of manufacturing and logistics. A very good explanation can be found in the Forbes article, What is Industry 4.0? . In short, where Industry 3.0 was enabled by computerization, Industry 4.0 takes that computerization and adds communications’ networking to it to completely revolutionize manufacturing and logistics as we know them.
MEF 3.0 PoC (126)—led by Amdocs and Cisco—demonstrates this to great effect in the context of MEF 3.0 and shows the huge potential for Communications Service Providers to offer industry customers solutions that neither System Integrators nor OTT Cloud Providers can. Many of us may think that networking in manufacturing is all about getting all those robots in the factory to work more effectively. However, this PoC introduces a much richer and broader vision than that of just liberating factories from network cables. It shows that products today often have their ‘connected’ lifecycles begin right at the beginning of the manufacturing process and extend seamlessly through production to being embedded in the service delivery to the end user.
To gain further insight on these opportunities, Daniel Bar-Lev, Director Office of the CTO, MEF discussed the PoC with Mark Gibson from Amdocs—one of the PoC leaders—to highlight this new market and its high business value and relevance to both enterprises and service providers.
Interview
DBL: Mark, please tell us briefly about Amdocs.
MG: Amdocs is a market leader in solutions and services for communications and media companies, including digital business managed services. We have a very broad range of offerings in this space—too many to mention here—but it’s important to mention why we are in MEF: We have very strong service orchestration implementations of MEF LSO, as evidenced by our pioneering work with AT&T on ECOMP and what became ONAP. Perhaps more pertinent to this PoC, we now have a strong involvement in 5G, including on the radio and eSIM side. In fact, we already have around 500 5G radio support specialists and 125,000 radio sites under our day-to-day management. We are also an FCC-accredited SAS (Spectrum Access System) provider with our SpectrumONE solution, enabling CSPs to acquire CBRS spectrum, as needed.
DBL: The title of the MEF 3.0 PoC (126) includes the term ‘5G Factory’. Is that just a neat way to use a buzzword to get attention for your 5G offerings?
MG: Definitely! Seriously though, 5G is a very important aspect of enabling Industry 4.0. Wired connectivity is too limiting in many manufacturing environments. Products and tools are moving around during many manufacturing processes and plugging them in each time they move isn’t going to scale. Therefore, wireless connectivity is a must. The Thing in IOT can be what’s being fabricated as much as the machines doing the making.
DBL: Aren’t WiFi or 4G sufficient? Why 5G?
MG: WiFi’s limitations in an Industry 4.0 environment are that the performance isn’t sufficiently deterministic for things like scheduled tasks and there’s a major issue of moving between WiFi access points, which means the performance can vary dramatically as the connected device moves around the factory. 4G doesn’t deliver the performance that is increasingly needed for highly granular activities such as a robot doing very fine movements that require, say, 1ms latency. 5G does deliver the required performance and more, so it’s the best starting point for wireless connectivity in the Industry 4.0 factory.
DBL: So, can’t system integrators set up 5G environments in the factory? What advantage does a CSP as a partner have here from the point-of-view of the manufacturer? The PoC title includes the term ‘Private Enterprise Networks’ so it sounds a bit like they are enclosed insular environments.
MG: It is true that a Private Enterprise Network is intended to be just that—deployed for the sole use of that enterprise. Roaming tends to be explicitly prohibited and the network itself will be tuned to perform the specific operations needed on the Enterprise site.
In some cases, it’s also true that the radio equipment that is proposed in the factory use cases is intended to deploy like an enhanced version of WiFi. But, there are also deployment scenarios in which capabilities like network slicing in the service provider network, across a specific location, can be used to deliver the required QoS for the relevant factory use-cases.
However, most importantly, once you start running mission critical operations on that infrastructure, you want to be backed up by a partner that is used to running those sorts of operations day-in and day-out. CSPs have that experience maintaining their own infrastructure and there is a great deal of synergy with the enterprise space, not least as many of them are already offering managed services for fixed networks.
DBL: Is the last aspect the advantage that CSPs offer to enterprises over OTT and SI players?
MG: Yes, exactly. Many CSPs have very rich and highly distributed communications assets that are finely tuned to the needs of enterprises. It is much easier for a CSP to tie in a 5G setup, in a specific manufacturing facility, into an overall application solution across the region, or internationally.
DBL: Take me through an example of a manufacturer creating a 5G factory that illustrates these capabilities.
MG: Imagine a global car manufacturer that is revitalizing a car plant in Detroit. The manufacturer is introducing a new model of hybrid car with extensive computing and connected capabilities. Not only does the manufacturer want to use the latest and highly accurate robotics during the manufacturing process, but they want to ‘inject’ software into the car’s computers even before it has been completely assembled. The car is moving around the factory floor with its compute capabilities being added to and tested using 5G wireless technology. In fact it may have one or more eSIMs embedded in order to give the car and its parts an ‘identity’ in the overall manufacturer’s and supply chain partners’ international systems so that they can track progress and deal with issues as soon as they appear in the process.
Once the cars have been completed, they are ‘released’ for delivery to customers. Their connectivity continues seamlessly outside the factory walls. And, once at the dealer, the private 5G eSIM can roam onto the local network and a full diagnostic of the car can happen as the driver is signing in and choosing which type of coffee to drink. Manufacturers are increasingly treating cars as vehicles for offering transport services, including pre-emptive maintenance and pay-as-you-go usage that will rely on 5G connectivity throughout the car’s lifetime.
DBL: Sounds very compelling for complex computerized products like cars. But what about a simple bottling plant or a wood panel manufacturer? Do they need a 5G factory?
MG: Definitely, it offers all manufacturers a lot of potential value. Think of security camera systems, which every factory needs nowadays. It’s not enough to capture and store video, and have security guards monitor screens. Security video today needs to be streamed to the cloud for automated processing and triggering actions by security services, etc., remotely. We envisage CSPs being able to use the combination of 5G factories, network slicing and all their assets outside the factory to, not only deliver the primary services mentioned within the factory, but also to innovate countless derivative services that are enabled by 5G.
DBL: One last question, Mark. What’s the unique differentiator of the work of MEF and MEF 3.0 for Industry 4.0 and the CSPs serving these use cases?
MG: In short, MEF-defined services, network slicing, and UNIs. MEF has developed a very robust set of abstract definitions for orchestrated communications services and their components, which makes it much easier for a service provider to interconnect the world of the 5G factory with the huge range of orchestrated connectivity-based services they offer, including into cloud architectures. In fact, we even envisage the use of MEF 3.0 SD-WAN services (defined in MEF 70) being used to provision and maintain the virtualized components of the 5G infrastructure. The possible uses and combinations of use of MEF 3.0 work for Industry 4.0 are only beginning to be understood.
MEF 3.0 PoC (126) – 5G Factory – Private Enterprise Networks for Industry 4.0 will be showcasing at MEF19 November 18-20 in Los Angeles.